Product Responsibility
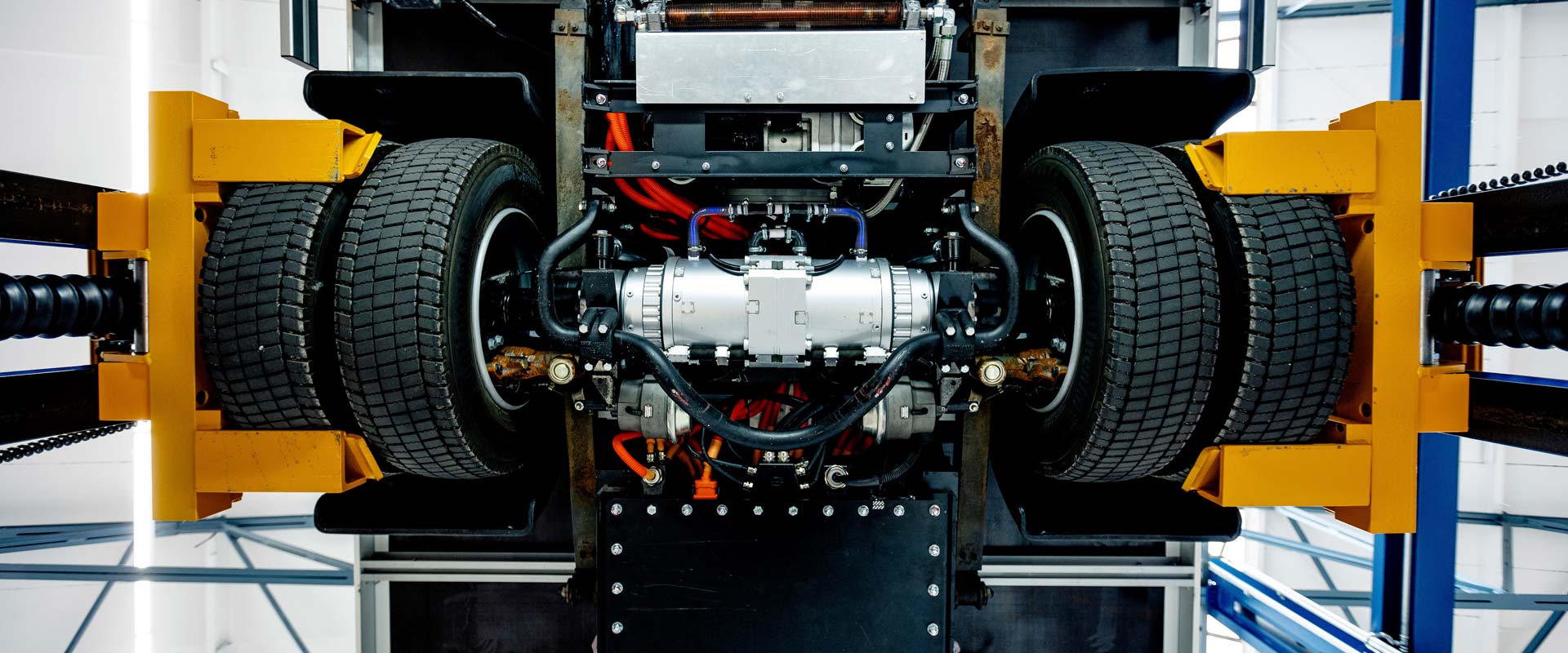
Holistic thinking – for holistic solutions
A prime example of this holistic thinking is the new ‘ECO Air’ running gear generation. The running gear and axle systems are now produced digitally. They are more modular and can be used with greater versatility, whilst also being lighter and therefore more economical than ever. Their digital DNA ensures more efficiency throughout the entire life cycle – from configuration through to maintenance and spare parts ordering.
Modularity
BPW development engineers design the interfaces between components so that everything can be quickly and easily replaced. The modularity means that BPW running gear systems are also optimally equipped for the future.
This reliability and ease of repair explains the low operational costs and the high resale value of vehicles with BPW running gear: this is sustainability that pays.
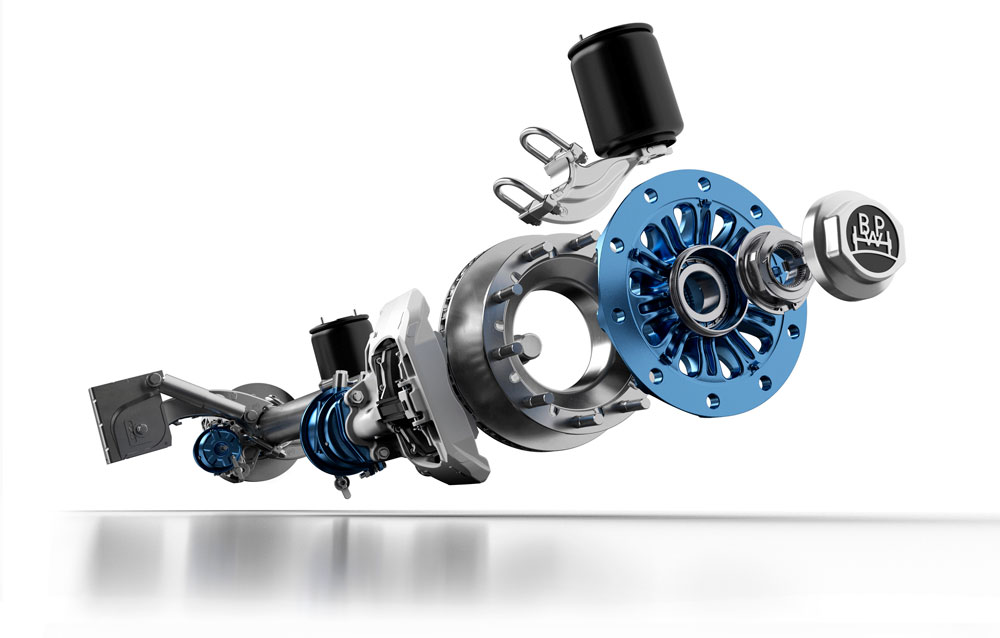
Running gear that delivers savings: lighter vehicles, greater usable load, reduced emissions

Saving of 27 kg: the new ECO Air running gear generation
Saving of 54 kg: the BPW alloy hub
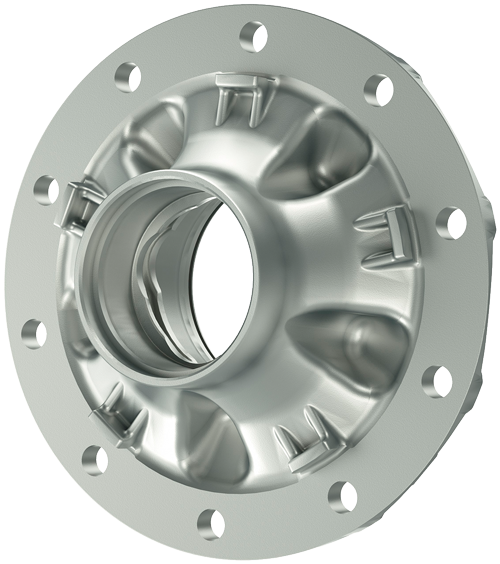
Saving of 39 kg: the Light Tube trailing arm
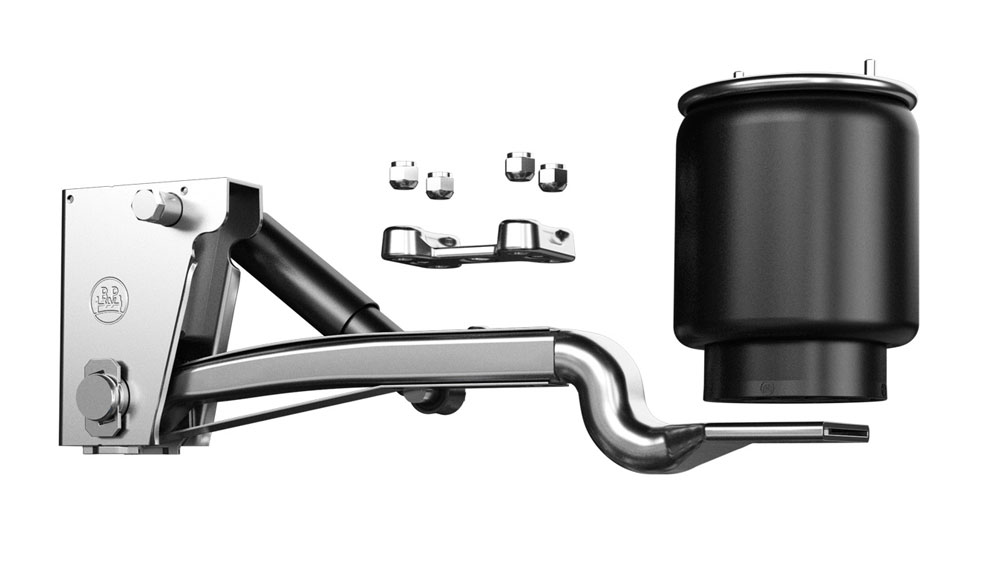
Transporting more efficiently, more safely and more intelligently with sensors
Accidents, diversions, thefts of cargo, as well as driving styles that consume materials and fuel are damaging for the climate and the environment – and cost the transport industry billions every year.
BPW and idem telematics are making the entire transport process more transparent, safer and more efficient with mechatronic innovations and the networking of drivers, freight and vehicles.
Sensors for load securing
BPW has developed the iGurt as a load securing system that displays and documents the correct tension when cargo is being secured and throughout the journey. If the forces deviate, the driver is informed via a smartphone app. The solution was developed in close collaboration with hauliers and drivers and has been awarded numerous innovation prizes.
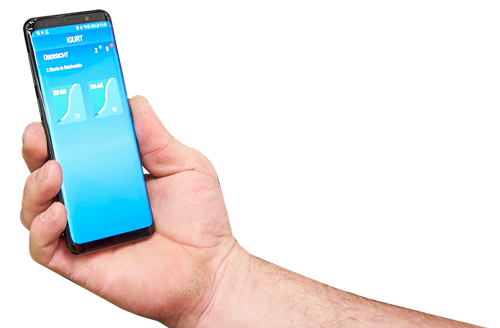
Sensors to save materials and fuel
The AirSave system also prevents vehicle and delivery failures, protects the environment from unnecessary emissions – and reduces the number of discarded blown tyres at the side of the motorway
Sensors for safe manoeuvring
Combined with intelligent sensors and mechatronics, the trailer also makes light work of reversing. The new Active Reverse Control provides fully automatic control of the steering angle for reverse manoeuvres and is easy to retrofit – and it is now also available for low loader trailers. Drivers can now safely steer drawbar trailers in reverse: narrow loading ramps, petrol stations and other accident-prone driving situations no longer pose any problem.
Networking – for optimised use of energy and resources

TC Trailer Gateway PRO: networking without a tangle of cables
And the more systems there are in use, the more efficient – and more environmentally friendly – transport becomes.
TC Solar: networked with the sun
CargoTracer: networked flows of goods and synchronised production processes

The BPW Innovation Lab has now developed the CargoTracer system, which is so inexpensive, straightforward and versatile that it not only networks transport processes, but also uses a new ultra-narrowband radio network to locate vehicles or even other moving objects.
This may include, for example, expensive construction machinery – or valuable, specially made carriers that need to be transported back to the sender but are often accidentally left with the recipient and forgotten.
The settings for when, where and how often the CargoTracer sends reports can be individually configured. As it only needs small amounts of data for this, the system is low-cost and energy-efficient, and the battery lasts for around five years.
Electromobility: diesel is out; the electric axle is in
City logistics is a highly promising area of use: the CO2 emissions of delivery vehicles in the 7.5-ton class amount to around 450 grams per kilometre in the inner city. That accounts for ten tons per vehicle annually, plus nitrogen oxides, particulates and noise pollution.
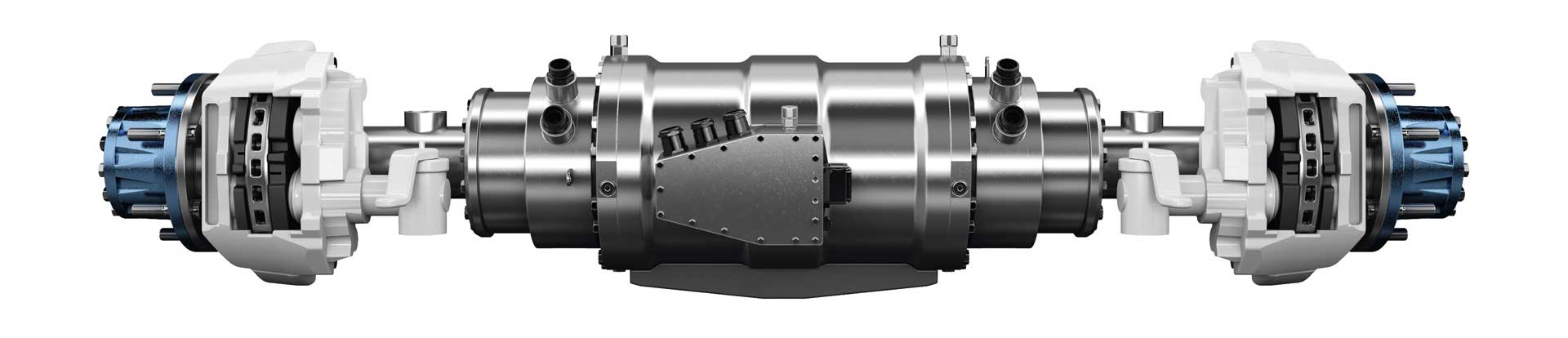
The efficiency will be increased even further in future as the vehicle will automatically detect its state of loading and will control the power required for this. BPW uses the battery systems of the BMWi3, which are powerful, responsibly produced and can be reused later, for example for stationary storage.
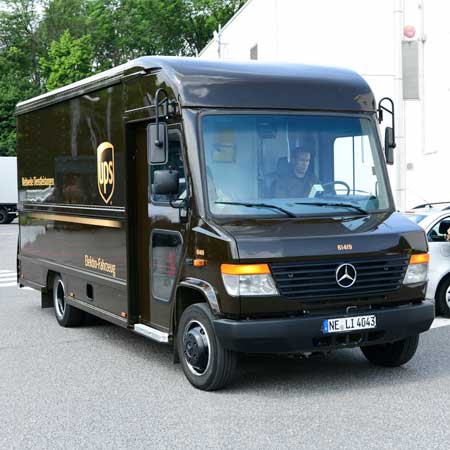
UPS: moving lab for CEP logistics
UPS and BPW are working together to test the use of the electric axle drive in central Cologne. Paul Nutzfahrzeuge has converted one of the familiar brown and gold 7.5-ton delivery vans from diesel to electric drive for the trial. With 3,290 newton metres per wheel, the drive technology from BPW produces almost ten times the torque of an average four-cylinder combustion engine and copes with the high payloads, heavy superstructures and steep gradients that are typical in municipal use.
Photo: Olaf-Wull Nickel
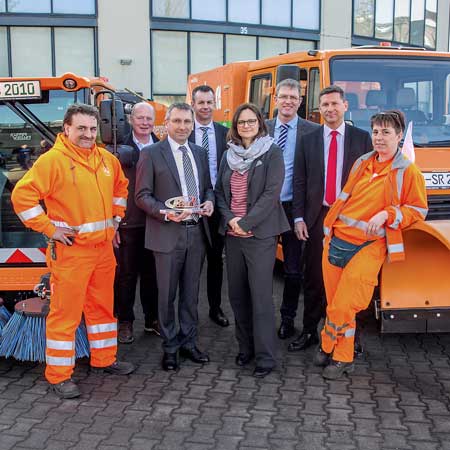
BSR and AWB: clean transport in the city
The specialist conversion company Paul Nutzfahrzeuge installs the BPW axle drive primarily in diesel to electric conversions of special-purpose municipal vehicles. The city waste management companies AWB in Cologne and BSR in Berlin are already using their first converted vehicles. The conversion is proving worthwhile as it gives the expensive vehicles a second cost-effective and zero-emission life – eliminating the need for fuel, lubricants and expensive maintenance intervals. During the conversion, the interiors and exteriors of the vehicles are refreshed and they can then be used for many more years.

Hellmann: electric mobility in general freight logistics
How do electric delivery vehicles work in general freight logistics? How can the logistics processes be optimised for this? Hellmann Worldwide Logistics, Osnabrück University of Applied Sciences and BPW are using a field test to investigate the use of an electrically powered van in various topographies and with varying trip configurations for inner-city deliveries in the German towns of Lehrte, Osnabrück and Bielefeld.
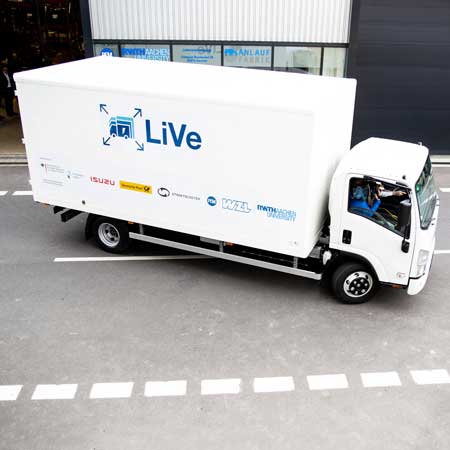
RWTH Aachen University: modular zero-emission truck
Researchers at RWTH Aachen University are developing a modular system for the electric truck of the future. Its centrepiece is the electric drive axle from BPW. For this project, the ‘Chair of Production Engineering of E-Mobility Components’ (PEM) at RWTH Aachen is working with Isuzu Motors Germany, StreetScooter and the RWTH Aachen machine tool lab. The project is funded by Germany’s Federal Ministry for the Environment, Nature Conservation and Nuclear Safety through the ‘Renewable Mobility’ programme.
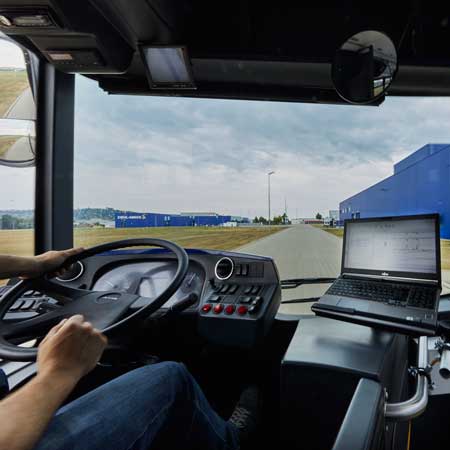
Ziehl-Abegg: BPW portal axle for electric buses
With the ZAwheel electric hub drive, ZIEHL-ABEGG is enabling energy-efficient drive systems for buses, without diesel fumes and noise. The drive is suitable for use as original equipment and in conversions for city buses, airport buses and double-decker sightseeing buses. BPW developed a compact low-floor portal axle for ZIEHL-ABEGG so that the electric drive can be delivered as a complete axle drive module ready for installation.
Supplier management:
product responsibility only works in a team
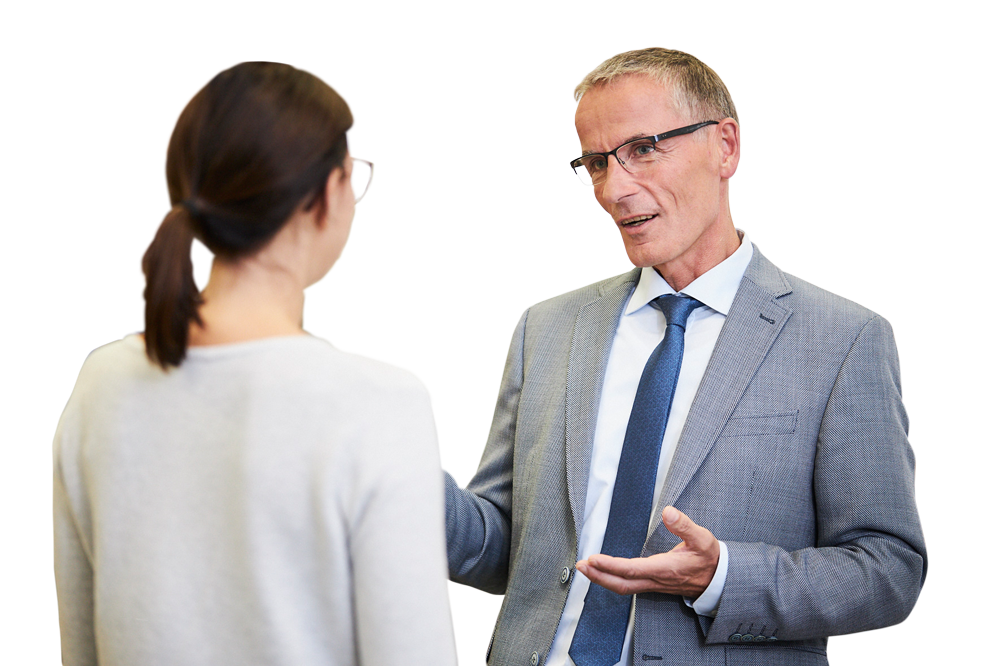
BPW also expects continuous improvement in environmental efforts, such as compliance with DIN ISO 14001 and/or Regulation (EC) No. 1221/2009 of the European Parliament and of the Council (EMAS). BPW partners also commit to the RoHS EC directives and REACH Regulation, which prohibits the use of hazardous substances. In 2019, BPW expanded its supplier contracts and purchase conditions to also cover children’s rights and child labour.
New criteria for the supplier audit
The supply chain managers audit up to 50 suppliers every year and they began applying the new criteria in spring 2019. By the end of 2019, around 15 per cent of suppliers will be audited in line with the new requirements and it is expected that all suppliers will be subject to the new audit criteria by 2025.
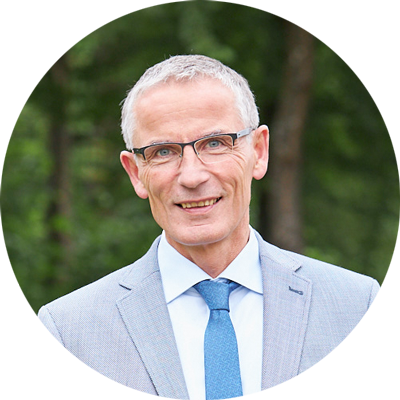
‘In SCM, we also look at our suppliers’ sustainability in our audits. We conduct 40 to 50 audits per year to verify, for example, whether they comply with the ban on child labour, whether legally relevant laws and regulations are being upheld, whether they guarantee occupational safety and to what extent our CSR initiatives are in effect with the supplier.’
Certified: quality at the highest level in the automotive industry
BPW is certified to IATF 16949:2016 and so fulfils the highest standards of quality in the automotive industry with respect to product, process and service quality. Certification confirms that the company fulfils comprehensive requirements with regard to risk management, compliance, environmental protection, energy use and occupational safety, among others. Beyond commercial vehicle industry standards, the IATF standard itself is the highest level in the automotive industry. The BPW Group specialist in composite material solutions, HBN-Teknik from Denmark, has also been certified in accordance with IATF 16949:2016 since June 2018.